Low-Metallic Brake Pad Manufacturer
- Reliable Stopping Power
- Reduced Brake Fade
- Minimal Brake Dust
- Low noise and vibration for a smoother ride
Low-Metallic Brake Pad Manufacturer
As a professional low-metallic brake pad manufacturer in China, our GDST specializes in a wide range of vehicles – Japanese, Korean, European, and American models. Whether it’s for passenger cars, SUVs, or trucks, our products are made to meet your needs.
We focus on quality from the start. Our low-metallic formula delivers stable braking performance, good heat resistance, and reliable wear life. It’s a great choice for customers who want consistent performance at a reasonable price. Every batch is tested carefully to ensure it meets high safety and performance standards.
Over the years, GDST has built long-term partnerships with customers in more than 100 countries. We understand what distributors and wholesalers need: dependable quality, competitive prices, and on-time delivery.
If you’re looking for a brake pad supplier you can count on, GDST is ready to support your business.
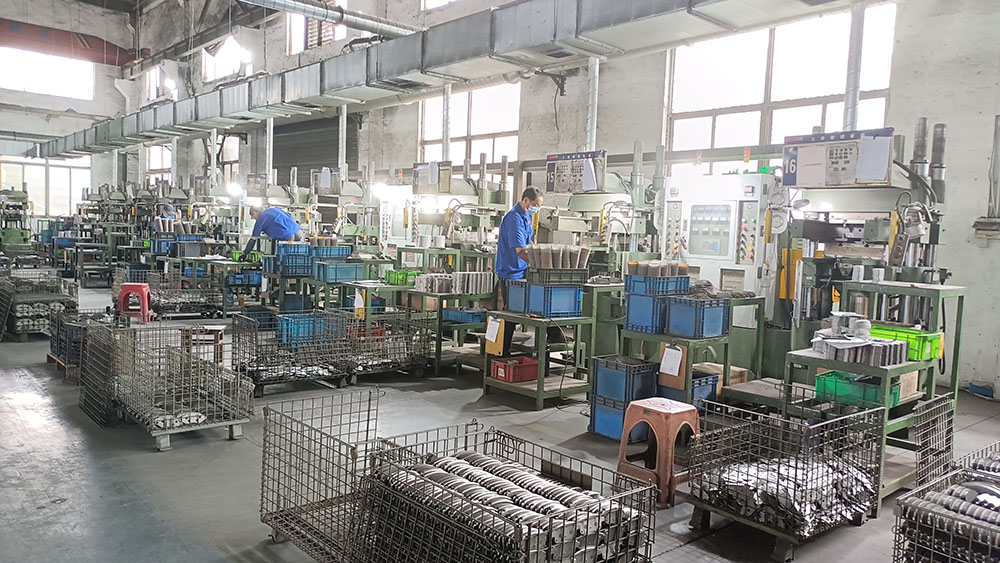

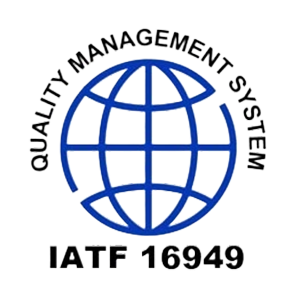
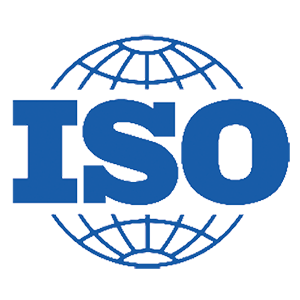
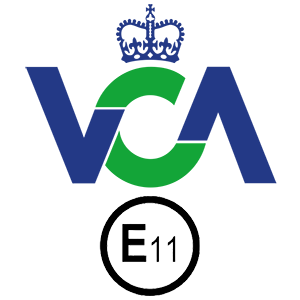
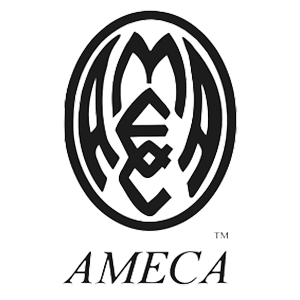
GDST Low-Metallic Brake Pads


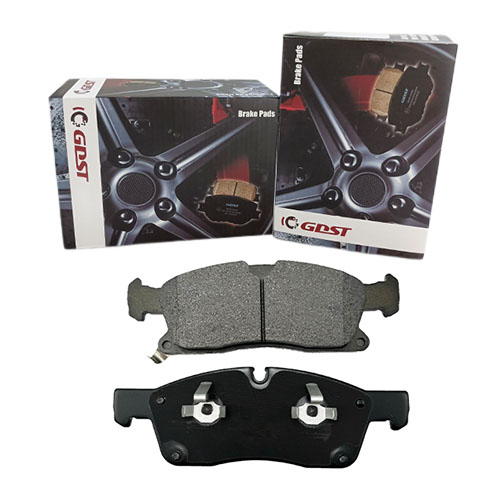
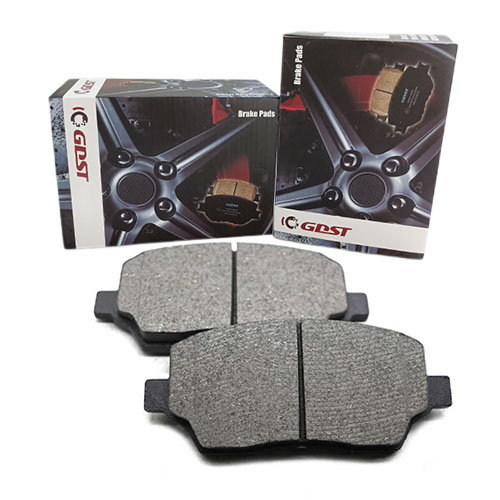
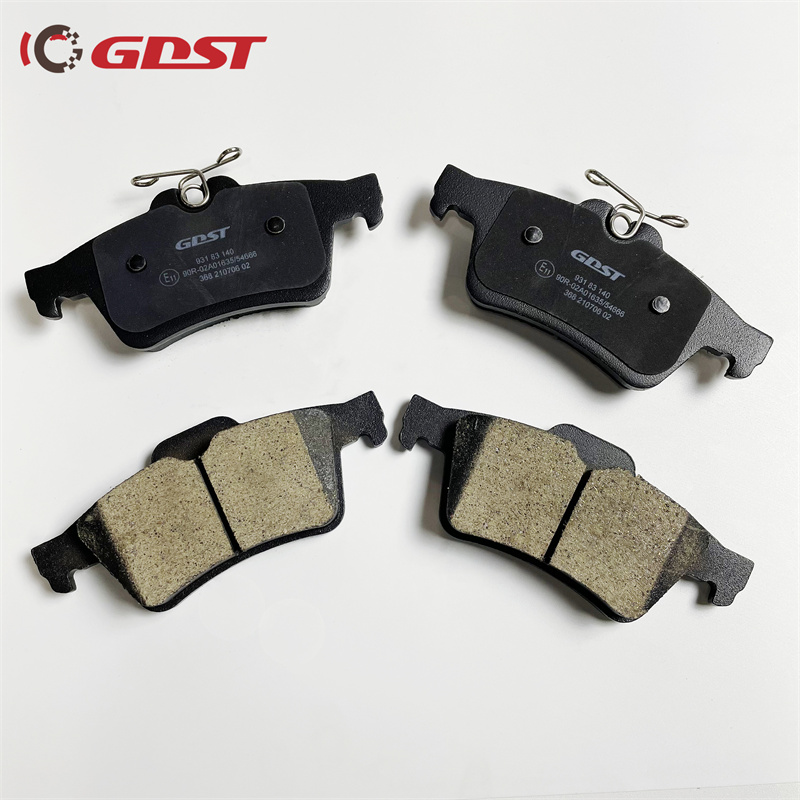

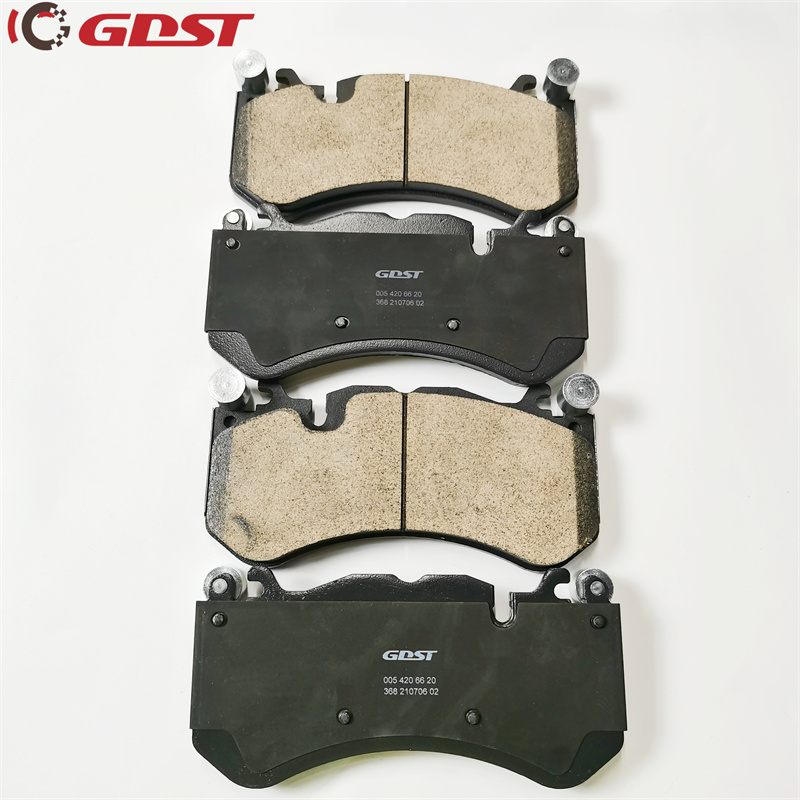
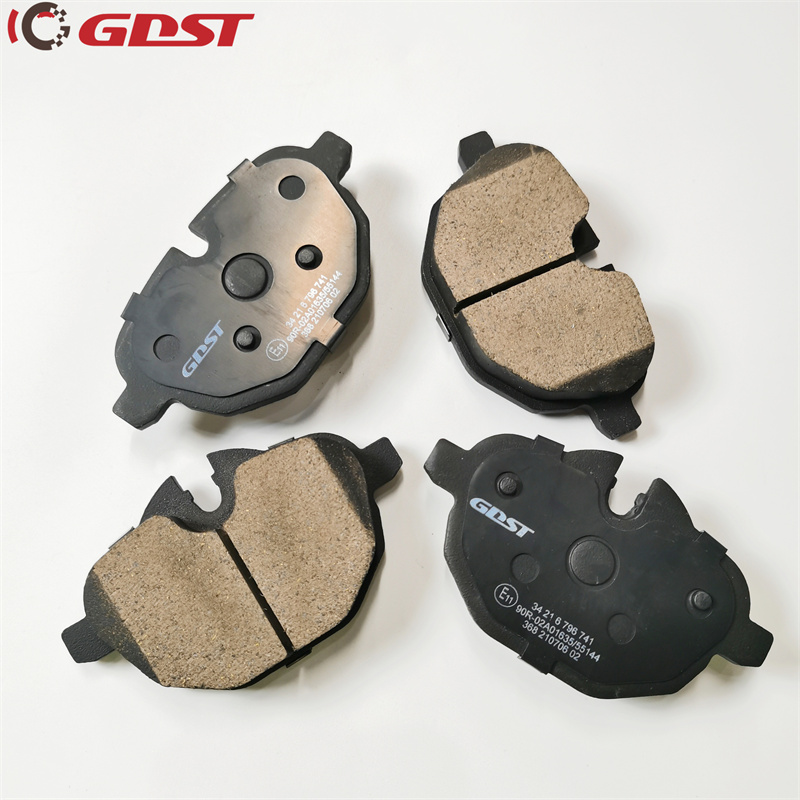
GDST Low-Metallic Brake Pads Formulas
We have rich experience in the production and sale of brake pads. Low-metal materials have different levels. Different markets require different brake pad materials. You are welcome to consult us at any time!
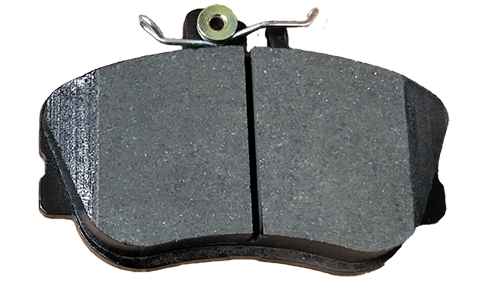
- Stable low-metal formulations
- Popular in the Middle East and Africa
- With 100% customer satisfaction
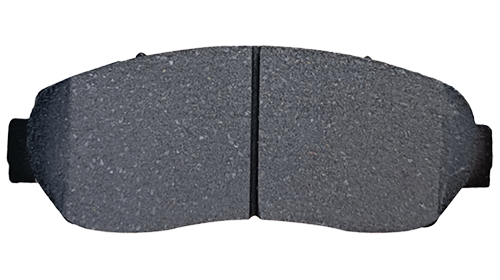
- Stable low-metal formulations
- Popular in the Middle East and Africa
- With 100% customer satisfaction
How Long Low-Metallic Brake Pads Should Last?
Low-metallic brake pads usually last between 30,000 and 70,000 kms. If you're often driving in stop-and-go traffic or carrying heavy loads, they might wear out faster. But if you're mostly on highways, you can get more life out of them.
Low Metallic vs Ceramic Brake Pads
Low-metallic brake pads are great for stopping power and heat dissipation but tend to be noisier and create more brake dust.
Ceramic brake pads, on the other hand, are quieter, produce less dust, and last longer, but they might not handle heat as well under extreme driving conditions.
If you want performance, go for low-metallic; if you prefer comfort and cleaner wheels, ceramic pads are a solid choice.
Low Metallic vs Semi Metallic Brake Pads
Low-metallic brake pads give you good stopping power and handle heat well, but they can be a bit noisy and dusty.
Semi-metallic pads are more durable and work better in tough conditions, like heavy braking or colder weather, but they also tend to be louder and wear down the rotors faster.
If you're after strong performance, semi-metallic is the way to go, but for everyday driving with less noise, low-metallic pads might be a better fit.
Brake Pad Shim Materials
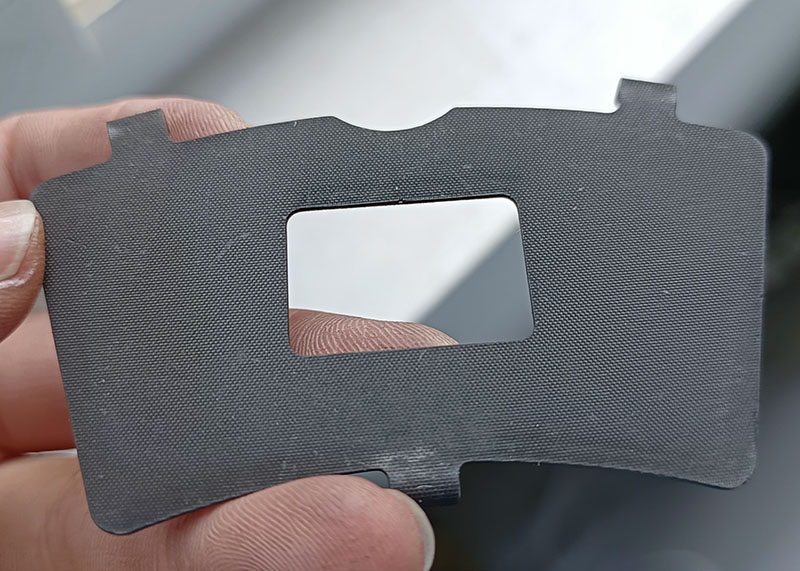
Cloth Anti-Noise Shim
Made of fiber or woven material for basic noise reduction. Cost-effective and suitable for standard driving conditions. Used in economy vehicles and general aftermarket brake pads.
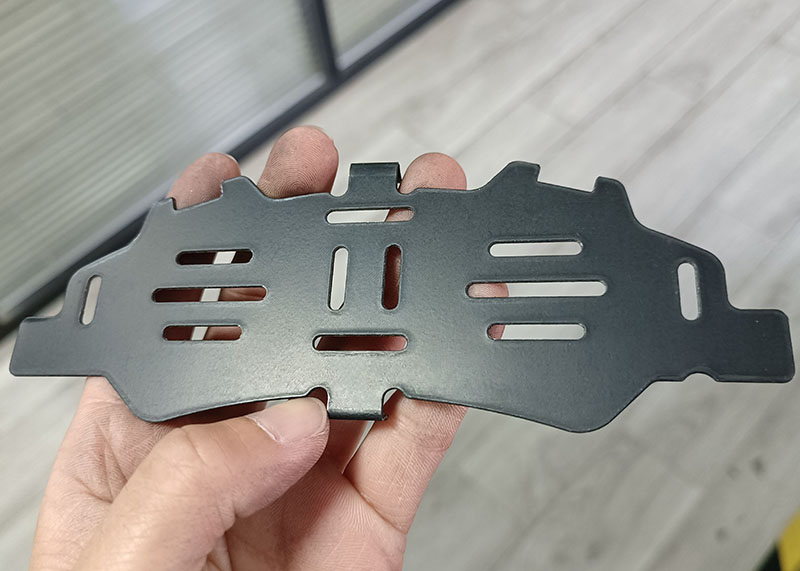
Rubber Anti-Noise Shim
Rubber-coated steel shim provides excellent sound and vibration dampening. Offers quiet braking and comfort in daily driving. Common in OEM and high-quality aftermarket pads for passenger cars.
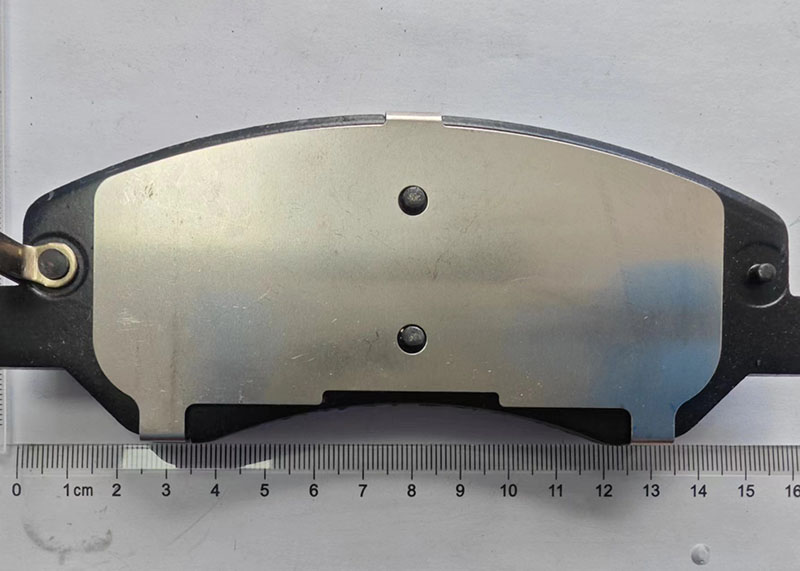
Stainless Steel Anti-Noise Shim
Durable metal shim that withstands high temperatures and pressure. Long-lasting and ideal for heavy-duty performance. Used in trucks, SUVs, and high-performance or premium brake pads.
Why Work With GDST?
Lower MOQ
100set/model
Competitive Price
Factory Direct Selling
Warranty
1 Year/30000kms
Fast Delivery Time
40-45 days on time
Free Sample
Test quality before ordering
Widely Application
Do you need brake pads for Japanese, Korean, European, and American vehicles? You’re in the right place. We’ve got you all covered. With such wide coverage, we make it easy for you to buy everything you need from one reliable supplier.
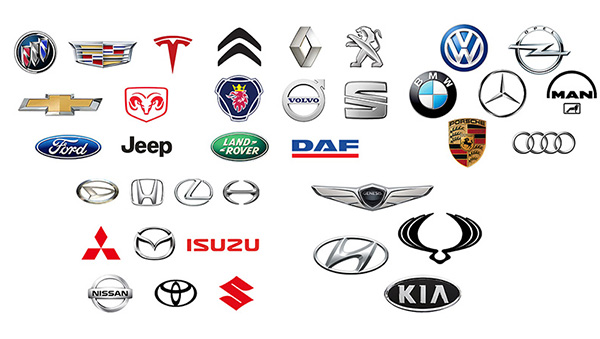
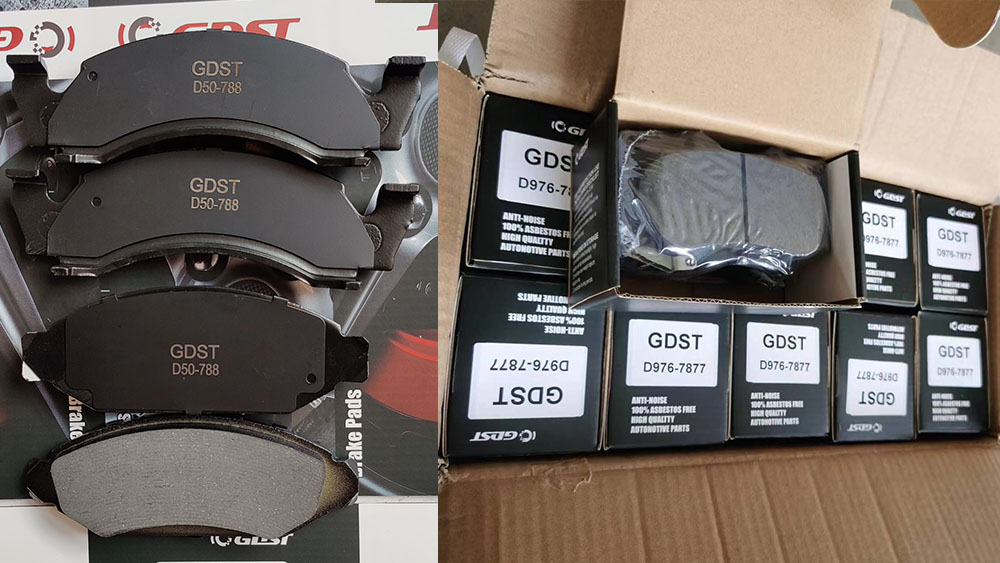
OEM & ODM Service for Your Brand
If you need low-metallic brake pads that aren’t in our current range, we can produce them based on your samples. We’re here to support your unique product needs.
We also offer full branding support to help your products stand out. Whether it’s printing your logo or creating attractive packages that reflect your brand’s style, we make sure every detail supports your market presence and helps you win more customers.
Reliable Quality You Can Trust
We take quality seriously. That’s why our brake pads go through advanced NVH Dynamometer testing to mimic real driving situations. The result? Brake pads that perform smoothly, stay quiet, and last longer—giving your customers the kind of reliability they expect and helping you build trust in your brand.

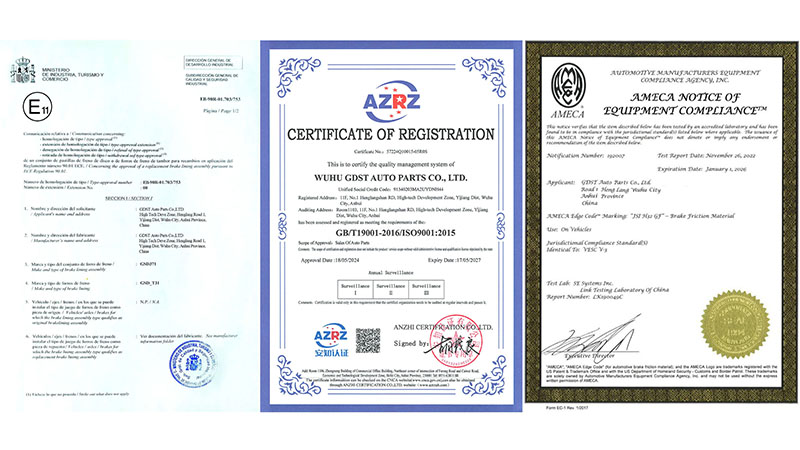
Certified Low-Metallic Brake Pad Manufacturer
Our production meets international standards, backed by certifications like ISO, IATF 16949, E-mark, and AMECA. These approvals reflect our focus on quality and consistency. When you work with us, you’re choosing a low-metallic brake pad manufacturer that meets global market requirements—giving you fewer quality issues, greater customer satisfaction, and more confidence in every sale.
Trusted by Customers in Over 100 Countries
With customers across more than 100 countries, we’ve gained deep insight into the demands of various markets. When you choose GDST, you’re teaming up with a low-metallic brake pad manufacturer that’s not only experienced but also trusted worldwide – ensuring clear communication, reliable delivery, and products that match OE quality.
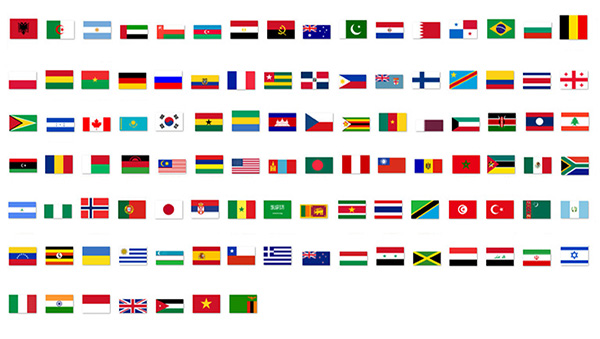
GDST Low-Metallic Brake Pad Factory
10+ Years History
Since 2011, GDST has been manufacturing low-metallic brake pads in one of China’s major automotive hubs, leveraging skilled labor, dependable supply chains, and advanced equipment to ensure efficient and consistent production.
Strict adherence to global standards like ECE, JIS, and ISO helps ensure the products meet diverse market expectations. Over the years, the brand has grown steadily, building trust with customers across continents who rely on dependable brake solutions and professional support.
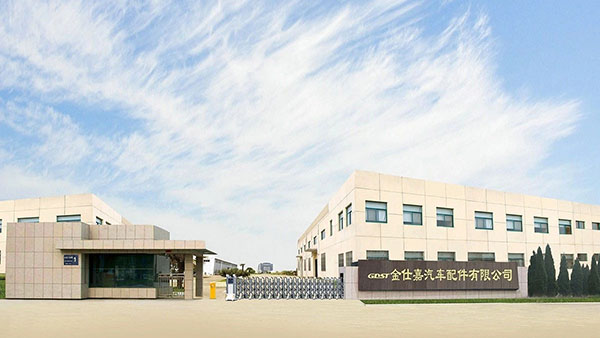
3000+ Brake Pad Moulds Cover All Your Need
We offer a comprehensive selection of over 3,000 low-metallic brake pad models, whether you’re looking for car brake pads or truck brake pads, we have you covered. Even if the model you need isn’t in our current catalog, we can develop custom molds based on your samples. With flexible production capabilities and complete one-stop service, GDST is your reliable low-metallic brake pad manufacturer to meet diverse market demands quickly and efficiently.

Robust Production Capacity to Power Your Growth
Our brake pad manufacturing facility spans over 20,000 square meters and is powered by a team of 100+ skilled workers. With well-equipped production lines and experienced staff, we ensure efficient manufacturing, stable lead times, and consistent product quality. Whether you’re placing a large bulk order or need a smaller, customized batch, our robust production capacity is ready to meet your needs – helping you scale your business with confidence.
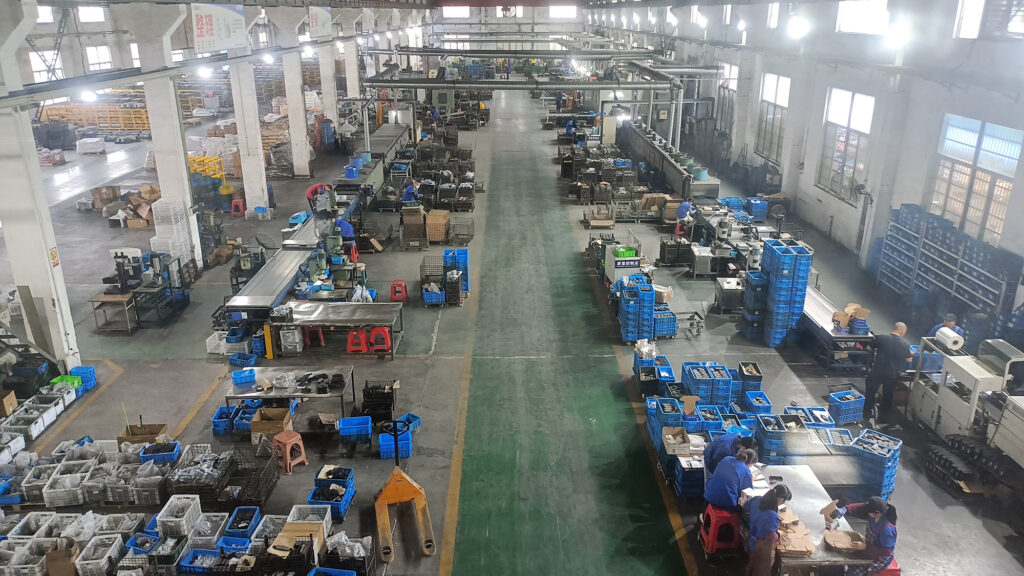
Advanced Quality Test Equipments
Quality is more than a promise—it’s a process. We apply a full set of advanced testing equipment to verify that each brake pad delivers reliable performance, long-lasting durability, and safety. From NVH dynamometers and shear strength testers to compressibility, wear resistance, and friction coefficient testers, each tool plays a critical role in our strict quality control. When you choose GDST, you’re choosing precision-engineered brake pads backed by proven technology and reliable performance.
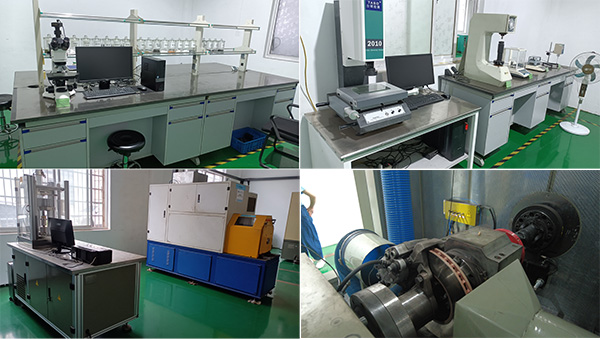
Production Process of Brake Pads
Step1: Precision Mixing with 800L Plough and Rake Mixer
The production of our low-metallic brake pads begins with a carefully controlled mixing process. Using an 800-liter plough and rake mixer, we blend key materials such as steel fibers, mineral wool, graphite, resins, and wear inhibitors.
Each formula is tailored to meet customer specifications, with the friction coefficient, wear rate, and noise levels precisely adjusted through the optimized ratio of raw materials.
This ensures that every batch delivers consistent performance and meets the desired quality standards.
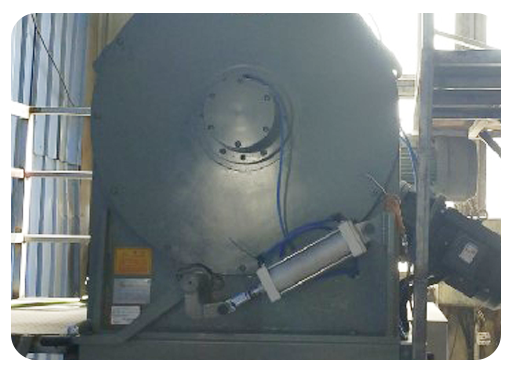
Step2: Brake Plate Preparation – Surface Cleaning, Shot Blasting & Gluing
Before friction materials are applied, the steel back plates undergo a thorough processing stage to ensure optimal adhesion and long-term performance.
First, each plate is meticulously cleaned to remove any oil, dirt, or contaminants.
Next, shot blasting is performed to create the proper surface roughness, enhancing the bond between the steel and the friction layer.
Finally, adhesive is applied with precise control over thickness and coverage, ensuring even application without any surface residue.
This careful preparation is key to the durability and safety of our brake pads.

Step3: Hot Forming Process and Heat Treatment
In this stage, the mixed raw materials are poured into molds and hot-pressed to form the initial shape of the brake pads. This process ensures a strong and precise integration of the friction material with the backing plate.
Once formed, the rough pads undergo a critical heat treatment—baked in an oven at high temperature for over 6 hours—to enhance material strength and stability. Each mold set can produce 6–8 pieces per cycle, and changing molds typically takes over 30 minutes.
This careful and consistent process lays the foundation for high-performance, durable brake pads.
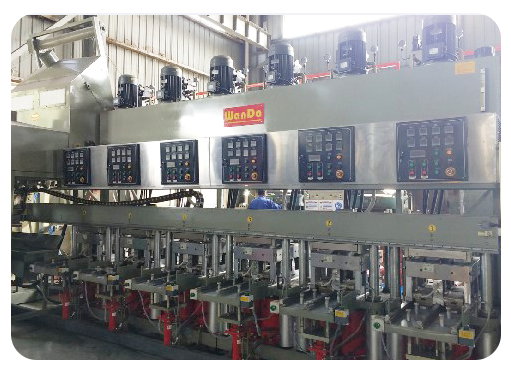
Step4: Grinding and Cutting for a Smooth Finish
After the heat treatment process, the brake pads often have surface burrs and uneven edges. To ensure a precise fit and smooth appearance, each pad undergoes grinding and cutting.
This step removes excess material, evens out the surface, and brings the pad to its final shape – preparing it for further processing and quality checks.
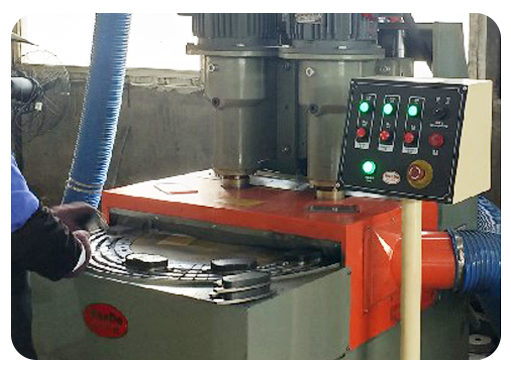
Step5: Machining – Slotting and Chamfering
To enhance the performance and safety of the brake pads, this stage involves precision slotting and chamfering.
Grooves are added to improve heat dissipation, reduce dust buildup, and optimize friction during braking.
Chamfering helps minimize noise and ensures a smoother contact with the brake disc.
Throughout the process, we carefully monitor the thickness and flatness of the pad surface using a linear grinder to ensure accuracy and consistency.
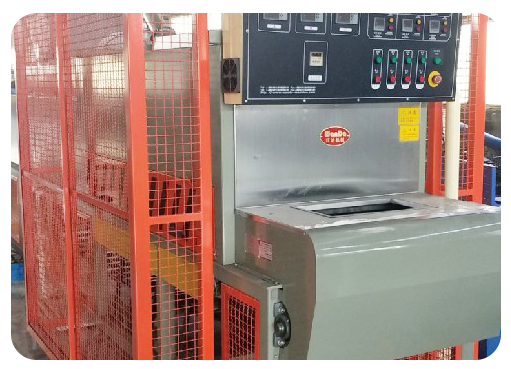
Step6: Painting – Rust Protection and Visual Finish
To protect the steel backing plates from rust and enhance the overall appearance, each brake pad undergoes a precision painting process.
We use electrostatic powder spraying – applying either flat or textured finishes – to ensure full and even coverage.
Key factors such as electrostatic voltage, oven temperature, baking time, and coating thickness are carefully controlled to achieve a durable, uniform finish that not only looks professional but also withstands harsh conditions.
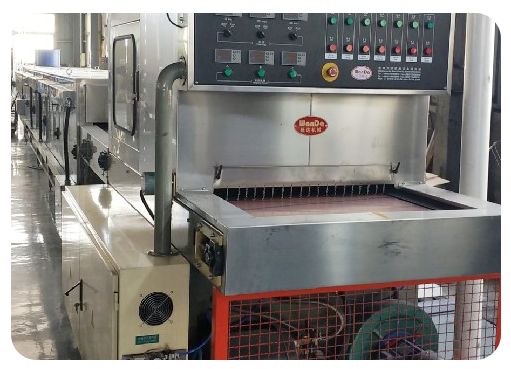
Step7: Final Assembly and Packaging
In the final stage, each brake pad is carefully assembled and prepared for delivery. We begin with pad printing and coding, marking both the friction material and steel backing with clear, precise identifiers. Attention is paid to positioning, size, adhesion, and clarity to ensure traceability and brand consistency.
Next, all necessary accessories—such as shims, wear sensors, springs, and clips—are installed with exact alignment and secure fastening. This includes rotary and pressure riveting, gluing, and checking for proper fit and durability. We also inspect critical features like alarm signal lengths, shock plates, and reinforcement blocks to guarantee functionality and safety.
Finally, each product is packed into individual color boxes, then grouped into cartons and secured on wooden pallets—ready for storage or shipment.
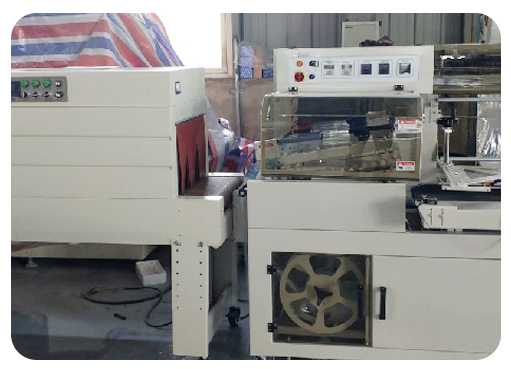
Customers Feeback
Our brake pads are trusted by customers from North and South America, Europe, the Middle East, Southeast Asia, and Africa. With stable quality and excellent service, we help partners confidently serve their local markets and expand their business.
Let GDST Boost Your Business Today!
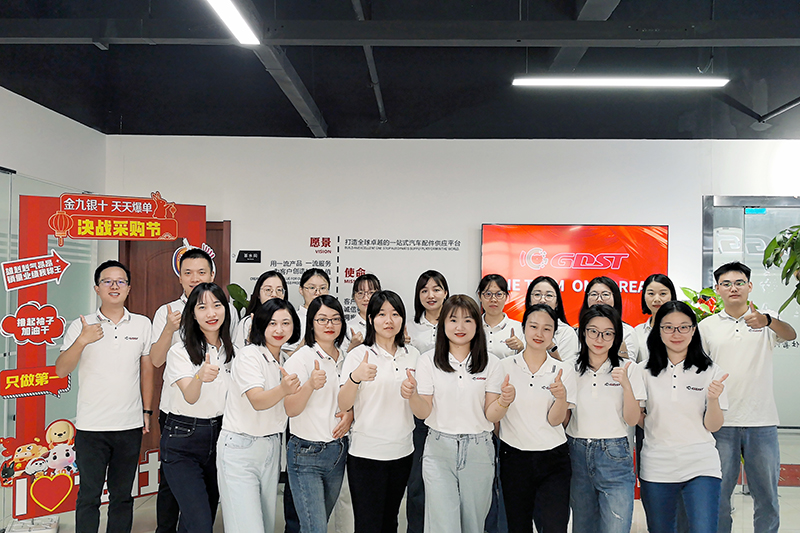
To help us provide you with accurate pricing and the right products, please send us a detailed inquiry list including:
- Part numbers (FMSI, ATE, OE, TRW, TEXTAR, etc.) along with the required quantities
- Preferred Material Type: semi-metallic, low-metallic, or ceramic
- With brake pad shims or without brake pad shims
If you have any special requirements, feel free to let us know – we’ll do our best to support your needs. Once we receive your list, our GDST team will get in touch with the best quotation asap